カテゴリ | 装置名 | 概要 |
---|---|---|
搬送・移載 | L字冷却コンベア | ラミネートチューブのL字平面搬送コンベアは、成形直後のチューブにキャップを締める際、開栓トルクが緩む問題と、強制冷却で成形部が収縮する課題を解決します。設置スペースが限られているため、L字での連続搬送が必要です。導入後、上流装置のサイクル速度に自動で追従し、多品種生産に対応可能となりました。海外製の上流装置との同期運転確認が現地でしかできず、トラブル対応準備が課題でした。サーボモータとエンコーダで同期運転制御を実現しました。 |
S字冷却コンベア | ラミネートチューブのS字平面搬送コンベアは、成形直後のラミネートチューブにおける打栓後の開栓トルク低下と成形不足を防ぐため、十分な冷却時間を確保しつつ連続搬送を実現します。導入後、上流装置のサイクル速度に自動で追従し、多品種対応が容易に。上流装置が海外製で運転確認が現地でのみ可能なため、トラブル対応準備が課題でした。サーボモータとエンコーダを使用し、同期運転制御を実現しました。 | |
インサート打抜装置 | 穴や形状を打ち抜く一般的な打抜装置とは異なり、結合された部品からひとつの部品を打ち抜き分解するための装置です。 部品をセットするための「可動式位置決め台」と打ち抜くための「パンチ機構」で構成されております。 多種の部品に対する汎用性があるため段取り替えの必要はなく、作業性向上や生産性向上にも繋がります。 |
|
ガントリーローダー | 24m間に直線状に配置した4台の旋盤・研削盤に順次シャフト素材を投入、加工後ストックしていくシステム。素材は全長130~370㎜、直径φ36~55と豊富なバリエーションを段替えレスで搬送できます。走行ローダーは1軸のみで極めてシンプルな構造で軽量化を図りタクトタイム短縮を実現しました。 | |
キャップ供給機 | キャッピング機にキャップを供給するタンク式昇降装置。 一度に何千個ものキャップ供給が必要となる為、オペレータのキャップ補給作業の回数を減らすために180ℓのタンクにキャップを貯め小出ししてパーツフィダへ安定供給を行う。 |
|
自動車部品搬送装置 | 自動車部品の加工工程間での搬送・移載作業を装置化することで、安全性と作業の安定性を確保しました。3種類の約30kgの製品に共用で対応可能な装置を設計し、段取り替えの手間や工数を削減しました。客先の要求に基づき、3種類の形状・寸法に対応した設計を行い、汎用性を持たせた装置を製作しました。装置はシンプルで高い剛性を備え、効率的な作業を支援します。 | |
デパレロボット | デパレロボットシステムは、パレット上の紙袋(900L×500W×200H、23kg)を真空吸着ハンドで把持し、下流の開袋機へ供給します。タクトは20秒/袋で、フォークリフトで2箇所のパレット置き場から供給されたパレットを、搬送コンベアで引き込み、リフトコンベアで開袋ラインに搬送します。パレット交換は、片方をデパレタイズしている間にもう片方を入れ替える方式です。紙袋の位置ズレにはパンタグラフ式チルト機構で対応し、吸着失敗時はパレット位置を調整してリトライします。 | |
樹脂材塗布機 | パーツフィーダから針状ワークを1本ずつ取り出し、インデックス上のコレットチャックにセット、塗布ステーションにおいてディスペンサーから吐出した樹脂コーティング剤を回転しながら塗布、次工程で熱風乾燥し、最後にコレットチャックから外して製品箱へ集積します。 | |
パイプ自動送り機 | パイプをメタルソー切断機に定寸ピッチで自動供給(送る)する装置です。 定尺パイプ1本分を自動供給できるように装置化したことで、都度のパイプの定寸供給作業の手間と負担が軽減され、作業者は別工程の作業も可能となり、作業性向上に繋がります。 |
|
ラミチューブ移載機 | ラミネートチューブを下流機に供給する搬送装置は、φ25~60のチューブを冷却チェーンコンベアから取り込み、下流の口元成型機に同期して移載します。4本集積後、速度を抑えて安定搬送を実現。導入後、上流装置と連動運転が可能になり、異常停止時には過剰供給を防ぐため空サイクルを設けました。製品に傷がつかないよう負担の少ない搬送を実現し、製品長さに応じた投入位置をタッチパネルで簡単に変更できる制御が可能です。 | |
ロボット箱詰機 | ラミネートチューブを通い箱に整列・集積する装置は、φ30~φ50・170Lのチューブを千鳥配列で確実に箱詰めします。箱のサイズやチューブの直径に応じて、スカラロボットが柔軟に対応可能です。導入後は、箱サイズ切り替え時間の短縮により、小ロット生産にも対応できました。ユーザーがロボットを初めて使用するため、復旧のしやすさを重視しました。品種切り替えを迅速に行うため、交換部品に位置決め機構を搭載し、簡単に調整できる設計にしています。 | |
ワーク移載装置 | 直立したワークを前工程から受入れる「搬送機構」と異なる搬送高さを解消する「昇降機構」を備えた移載装置です。 ワークはビンで破損の恐れが高いため、転倒検知や不足・衝突を回避する機能を有し、生産性を向上させております。 小型化したことで工場スペースの有効活用や生産時の効率化・省エネ・コスト削減にも繋がります。 |
|
ワーク印刷機 | 搬送治具にセットされた円柱状ワークの底面と側面にスタンプ式印刷機で識別番号を転写し、最終工程でUV照射してインクを硬化定着させる装置です。 搬送治具によりワークの位置合わせが容易で安定した印刷と、スタンプ式印刷機の採用により高精度で高品質な印刷が可能です。 またUV照射することで、インクの耐久性向上にも繋がります。 |
|
紙袋デパレロボット | 紙袋を開袋機に供給するデパレタイズロボットは、2種の原料紙袋を下流の要求に応じてデパレタイズする目的で導入されます。老朽化したロボットを更新するため、既存のロボット架台を流用します。ワーク供給は正袋(40袋)を簡易設定でパッチ供給し、処理能力は200袋/時、紙袋サイズは750×420×100mm、重量は25kgです。設置スペースは最小限で、既存架台に新しいロボットを設置する仕様となっています。 | |
ワーク移載装置 | 5種類の長さ400mm・1kg程度の自動車部品を研磨する工程の搬入・搬出コンベアを一体化した装置を設計し、段取り替えの手間を削減しました。装置化により、作業者は1.5時間程度の別作業が可能となり、効率が向上しました。5種類の製品に対応するため、長さやバランスに応じた支える位置やガイド位置を検討し、コンパクトな機構で破損防止を図りました。クーラント液対策としてオイルパンやカバーを使用し、安価で交換可能な部品を採用しました。 | |
樹脂部品組立検査装置 | 組み合わせたふたつの樹脂部品の「返し」付き勘合部に対して、はめ込みとはめ込み具合を確認する装置です。 感覚と力を要するはめ込みを自動化し、目視では見落としやすいはめ込み具合をセンサーで確認することで、省力化と品質向上に繋がります。 |
|
製品ストッカー | 上段部へ空パレットをストックし製品積み込み後にリフターで搬送、下段部へ満載パレットをストックする装置。 11段に積み上げてあるパレットは噛み合わせ状態となっており、最下面のパレットを次段パレットと切り離すために、最下面を吸着し固定しておき次段パレットに爪を挿入し引き離す構造としております。 |
|
反転移載機 | 2秒サイクルで上流プレス機から排出されるドーナツ状の冷間鍛造部品を天地反転させながら次工程プレス機へ連続で送り込む装置。 品番切替時も段替えレスで稼働し、限られた狭小スペース内で効率よく移載できます。 |
|
検査 | 振動試験治具 | 振動に対する感覚(触覚)を繊細に調べることでロボットハンドや人工手の開発に役立つ治具です。 センサーを取付けるための固定台と粘弾性の柔軟物を取付けるための固定台、振動を付加する振動発生器を取付けるための固定台で構成された治具です。 あらゆる接触具合や位置関係を振動付加状態で繊細に保てるため、振動と触覚に関する開発に役立つデータを詳細に得ることができます。 |
内外観検査システム | ラミネートチューブの印刷面や内面の汚れ、傷を検査する搬送装置は、高速ライン(150本/分)でキャッピング機から出てくる2系統のφ25~φ50×200Lラウンドチューブを1系統に合流後、1本ずつ回転させ、ラインセンサカメラで不良を検査します。OK品は箱詰め機へ、NG品は回収箱へ振り分けられます。内面・肩裏も回転しながら撮像検査が行え、目視検査では発見困難な不良も確実に排出できます。 | |
ニードル検査装置 | パレット上の筒状製品(240本/パレット)からスカラーロボットにて1本ずつ取り出し後、インデックステーブル上の治具にセットし、順次カメラ検査します。検査結果がOKであれば良品パレットへ、NGであれば不良品パレットへ再びスカラーロボットにて移載します。 | |
レーザーマーカー検査装置 | 材質セラミックのワークを次工程から受け取りレーザーマーカーにて刻印し刻印状態をカメラにて判別、不良品はシュートにて払い出し。 良品は受渡し後、ゲートカットを行い製品はコンベア上に開放。 レーザー刻印を行うU/T内はレーザー刻印により発生したカスをブロアにて吸引を行う。 |
|
樹脂部品組立検査装置 | 組み合わせたふたつの樹脂部品の「返し」付き勘合部に対して、はめ込みとはめ込み具合を確認する装置です。 感覚と力を要するはめ込みを自動化し、目視では見落としやすいはめ込み具合をセンサーで確認することで、省力化と品質向上に繋がります。 |
|
キャッピング | キャッピングライン | 樹脂チューブ(φ25~60、70~200L、マル・オーバル)にキャップ締めと外観検査を行う装置群では、オーバルチューブの外観検査を人手で行っていたが、カメラメーカーと協力し、治具や照明の工夫でオーバルチューブにも鮮明な画像を取得できるようにしました。また、キャップ締付けでの斜め勘合を減らし、歩留まり向上を目指しました。さらに、オーバルキャップの不安定な姿勢に対応するため、ユニットを水平配置し、バッファ機構を設けてラインの安定稼働を実現しました。 |
オーバル キャッピング機 |
オーバル・ラウンドチューブにキャップ締めするシステムは、φ25~60のラウンドとφ25~50のオーバルチューブに対応し、最速80本/分でキャップを組み付け、カメラ検査機能を搭載しています。インデックスモータを水平置きに変更し、キャッピング動作の安定性を向上させましたが、設置スペースに制約があり、コンパクトかつメンテナンス性の良い装置にするために工夫が必要でした。将来的な品種増加にも対応できるよう、機械・制御面で多くの工夫を施しています。 | |
キャッピング機 | ラミネートチューブにキャップを高速で打栓する装置は、φ33・38×100~200LのPONキャップ・チューブに対応し、150本/分のキャップ打込みが可能です。カメラやバーコード検査機能が搭載され、上流成型機との完全同期にも対応。導入前は2ラインで生産していましたが、1ラインに集約することで省スペース化・省人化を実現しました。設置スペースに制約があり、コンパクト化には苦労しましたが、将来の品種増加にも対応できるよう設計・制御に工夫を凝らしました。 | |
キャッピング機 (ブローチューブ) |
ブローチューブにトップシール貼付けキャップ締めを行う装置。 キャッピングは仮締めの後、増し締めして適正トルクを管理する。 Pシールの貼り付けを打ち抜き時に行うことで、貼付けの位置ずれが解消されました。 |
|
キャッピング機 (トップシール) |
ラミネートチューブにトップシール貼付けとキャップ締めを連続で行う装置は、80本/分でラウンドおよびオーバルチューブに対応します。Pシールの貼り付けを打ち抜き時に行い、位置ずれを解消。多品種生産に対応するため、溶着温度、溶着時間、押しつけ推力などを品種別に設定できるようにしました。トップシール貼付け、キャップ締め、画像検査を組み合わせた装置で、将来的な品種増加にも対応できる機械・制御の工夫が施されています。 | |
樹脂チューブ キャッピングシステム |
歯磨き粉のようなチューブ形状の容器にキャップを装着する装置です。 丸型と楕円形の2形状や押し込み・ねじ込み両タイプに対応可能です。 キャップ装着はもちろん、外観検査やコンタミ・逆胴チェックまで種々のキャップ形状に柔軟に対応できます。 さらに、オプションでバージンシール貼付や部分シュリンク、丸型改ざん防止チューブにも対応します。 |
|
冷却チェーンコンベア (アキュムレータ) |
ラミネートチューブをストック・常温冷却する立体搬送装置は、口元成形直後のチューブにキャップ締めを行う際の開栓トルク低下や、強制冷却による成形不良を防止します。 また、上流機・下流機の異常停止時にラインへの影響を最小限に抑えることができます。 導入後は、下流装置の異常停止時でも上流装置を止めずに生産効率を維持できました。 サーボモータとインダクションモータを使用し、周辺装置のサイクル変動の影響を回避した制御が実現されました。 |
|
治具・ハンド | クリップ組立治具 | 書類等を挟むクリップボードの挟み込み部分を組み立てるための治具です。 専用の治具を用いて作業できるようにしたことで、長時間作業による身体への負担軽減や組立時の不具合による作業効率低下を改善し、生産性向上に繋がります。 |
デパレロボット | デパレロボットシステムは、パレット上の紙袋(900L×500W×200H、25kg)を真空吸着ハンドで把持し、下流の開袋機へ供給します。タクトは20秒/袋で、フォークリフトで2箇所のパレット置き場から供給されたパレットを、搬送コンベアで引き込み、リフトコンベアで開袋ラインに搬送します。パレット交換は、片方をデパレタイズしている間にもう片方を入れ替える方式です。紙袋の位置ズレにはパンタグラフ式チルト機構で対応し、吸着失敗時はパレット位置を調整してリトライします。 | |
熱間鍛造移載ロボット | ドーナツ状に成型した製品を1000℃まで加熱後、多関節ロボットにて素早く圧延機から取り出し、冷めないうちに次工程へ搬送するシステム。圧延機の段替え作業も同じロボットでツールチェンジしたハンドにて自動段替えを実現しました。 | |
パレタイズハンド | ダンボール箱把持ハンド(片開き)は、箱の落下防止機構を追加するため、エアシリンダを用いて両開き構造に変更されました。箱のサイズは230~400×380~590×220~310mm、最大重量20kgに対応し、タクトタイムは15秒です。落下防止は、箱の側面から真空吸着方式で実現されており、段替えレスで対応できる設計です。 | |
樹脂成形周辺機器 インサートチャック |
数グラムの小さな金属部品を自動で成形機に挿入する装置を設計しました。部品形状が複雑で倒れやすいため、チャックの重量を増やせない代わりに、仮置き治具に倒れ防止機構を追加しました。金型内の隙間が狭いため、爪の形状を複数検討し、最適なものを選択しました。製品納入後の問題にも迅速に対応できる体制を整え、安心して使用できる装置を提供しました。 | |
樹脂成形周辺機器 ゲートカット装置 |
樹脂成型品(350x600x50、1kg)のゲートカットを行う装置を設計しました。取出チャックでワークを保持したままカットを行い、多種のワークに対応するため、各部品を調整可能にしました。これにより、様々な形状の製品にも柔軟に対応でき、安定した作業が可能となります。 | |
曲げ治具 | 加熱した樹脂ホースを曲げるための治具です。両端に口金がついたホースを加熱した後、半割れになった曲げ治具に沿ってロボットが3次元形状で曲げながらセットしていきます。曲げ完了後、口金から冷却エアーを流し、内部から冷却して形状を安定させます。 | |
マテハンロボット | バレティーナラックから円柱形鋼材(φ170:20kg~φ270:50kg)を供給ロボットで加工機に供給するシステムでは、ランダムに置かれた鋼材をカメラで位置検知し、ロボットが上面のみで把持します。タクトタイムは40分/個で、従来は人手で作業していたが、システム導入後はバレティーナをセットするだけで作業が開始できます。天吊りタイプのロボットを使用し、狭い作業エリアでも高い自由度を確保。段替えレス設計とし、電磁石やUSPによる電源バックアップも採用されています。 | |
緩衝材吸着ハンド | 緩衝材(段ボール製)をハンガーに供給するロボットハンドは、ストッカーから1枚ずつ取り出し、90度垂直に傾けてハンガーに掛ける作業を行います。ストッカーの積高さは最大1000mm、緩衝材の外径はΦ1400mmです。ワークの表面は凹凸があり、安定した吸着が難しいため、吸着技術の工夫が求められます。 | |
紙袋デパレロボット | 紙袋を開袋機に供給するデパレタイズロボットは、2種の原料紙袋を下流の要求に応じてデパレタイズする目的で導入されます。老朽化したロボットを更新するため、既存のロボット架台を流用します。ワーク供給は正袋(40袋)を簡易設定でパッチ供給し、処理能力は200袋/時、紙袋サイズは750×420×100mm、重量は25kgです。設置スペースは最小限で、既存架台に新しいロボットを設置する仕様となっています。 | |
紙袋吸着ハンド | 紙袋デパレタイズ用吸着ハンドは、紙袋を安定して吸着し、移載するために設計されています。紙袋が多少傾いていても安定して把持できることが求められます。搬送能力は200袋/時、紙袋サイズは750×420×100mm、最大重量は25kgです。把持力を高めるために、ブロア吸い込みによる真空吸着と、ダンパ切替による真空破壊方式を採用し、安定した吸着力を実現しています。 | |
振動・衝撃試験用治具 |
製品を振動試験機と衝撃試験機に取付けるために使用される治具で、「サイコロ治具」とも呼ばれます。 面積やねじサイズ/位置/本数が定まっている試験機の取付面に合わせた大きさで、ふたつの振動に耐えて試験に影響を及ぼさない材質と構造/形状となっております。 |
|
袋物ハンド | パレタイズ時にコンベア上の紙袋を確実に把持し振り回し中でも振り落とさない様に確実に紙袋を固定したい。 コンベア上でローラーピッチ隙間を狙い櫛型形状のハンドにて紙袋を救い上げる。 紙袋開放時は垂直落下させるために櫛が二重構造に配されている。 |
|
その他 | インサート打抜装置 | 穴や形状を打ち抜く一般的な打抜装置とは異なり、結合された部品からひとつの部品を打ち抜き分解するための装置です。 部品をセットするための「可動式位置決め台」と打ち抜くための「パンチ機構」で構成されております。 多種の部品に対する汎用性があるため段取り替えの必要はなく、作業性向上や生産性向上にも繋がります。 |
樹脂成型装置 | 板状軟性樹脂を加熱しながらプレスと成形をする圧縮成型機です。 樹脂を上下の金型に挟み込み、一定の圧力と設定温度をかけて指定の時間で圧縮成型します。 圧力と時間は任意で設定変更ができます。 多様な金型をバーコードで管理することで間違いを防ぎ、複数個同時に成型もできます。 |
|
接着剤塗布ライン | 化粧板を個室内装に貼り付けるため、化粧板の接着面に接着剤を自動で塗布する装置です。 化粧板は大きく、接着剤の乾燥を少しでも軽減するため、効率的に塗布できるように複数のガンを使用してます。 |
|
パイプ自動送り機 | パイプをメタルソー切断機に定寸ピッチで自動供給(送る)する装置です。 定尺パイプ1本分を自動供給できるように装置化したことで、都度のパイプの定寸供給作業の手間と負担が軽減され、作業者は別工程の作業も可能となり、作業性向上に繋がります。 |
|
ピン打込装置 | 樹脂製のフランジ付ピンにゴム製の円柱型ブッシュをエアシリンダーの動力を使用して打込み一体化させる装置です。 作業の場所を変更する場合があるため、コンパクトな卓上型で重さ約20kgとし、一般的な成人男性ひとりで持ち運べることが利点です。 |
|
シート供給機 | 現状は機械停止し人手にてシート供給を行っているため作業効率が悪い、シート供給を自動化するためにシート供給部をインデックステーブル上に配置し、次回分用のシートもセット出来る様にした。 シートを吸着する際、静電気で2枚目も付いてきてしまうため1枚づつ吸着出来るような構造とした。 |
|
ホース曲げロボット | 両端に口金がついたホースを1本ずつ回転式加熱炉へセット、一定時間加熱したホースをロボットが取り出し、空の曲げ治具に沿って3次元で曲げながらセットしていきます。曲げ終わったホースは、口金より冷却エアーを流して十分に冷やし、人が治具から外して完成します。 | |
メタルブッシュ巻き ローダー |
メタルブッシュを成型するために、原料となる帯材をプレス機に供給して排出する装置です。 装置化することで、人手での供給と排出がなくなり、安全性確保と作業率向上に繋げることができます。 |
|
自動車部品組立装置・ボール圧入装置 | マニホールドブロックのパス穴にボール(φ5鋼球)を圧入する装置は、大きな力が必要で人的作業では危険や不安定さが伴うため、自動化が求められました。圧入はプレス機で行い、姿勢変換は多関節ロボットで実現し、作業の安定化と労力削減を図りました。また、全体をカバーで覆い、安全性も確保しました。メンテナンスや修理時には工具不要で交換可能な構造とし、繰り返し精度を維持しました。川崎重工業様とのパートナー契約により、テストや試験対応も可能です。 | |
自動車部品搬送装置・刻印装置 | アルミ製の自動車部品(500x400x400・30kg)の加工工程で、人的な移載や姿勢変換の危険を避けるため、自動化された搬送・刻印装置を設計しました。部品製作から組立・単動確認まで行い、配管や配線の取回しを邪魔にならないよう配慮しました。特に、刻印ユニットやシリンダーの交換時に配管が邪魔しない経路を考慮し、安全かつ安定的な作業環境を提供しました。単動確認設備も完備し、要求圧力や動作確認が可能です。 | |
自動車部品搬送装置・姿勢変換装置 | 120kgある自動車部品の検査工程で、加工後に姿勢を垂直回転させて側面と裏面を検査する装置を設計しました。3種類の異なる形状・寸法の製品を安全かつ安定的に搬送・姿勢変更できるよう、段取り替えの手間を減らし、繰り返し精度を向上させる機構を採用しました。特に、縦横高さに差がある製品に対応するため、段替えなしで判別可能なコンパクトな機構を設計し、安全性と剛性を確保しました。将来の製品にも汎用性を持たせた装置となっています。 | |
廃物処理装置 | 不要となった廃物を肥料として利活用するために、廃物を大型のドラムに入れて間接的に温水と熱風をかけながら撹拌と乾燥をする装置です。 廃物を利活用することで環境にやさしく、一度に大量の廃物を処理できるため、生産性向上に繋げることができます。 |
|
反転移載機 | 2秒サイクルで上流プレス機から排出されるドーナツ状の冷間鍛造部品を天地反転させながら次工程プレス機へ連続で送り込む装置。 品番切替時も段替えレスで稼働し、限られた狭小スペース内で効率よく移載できます。 |
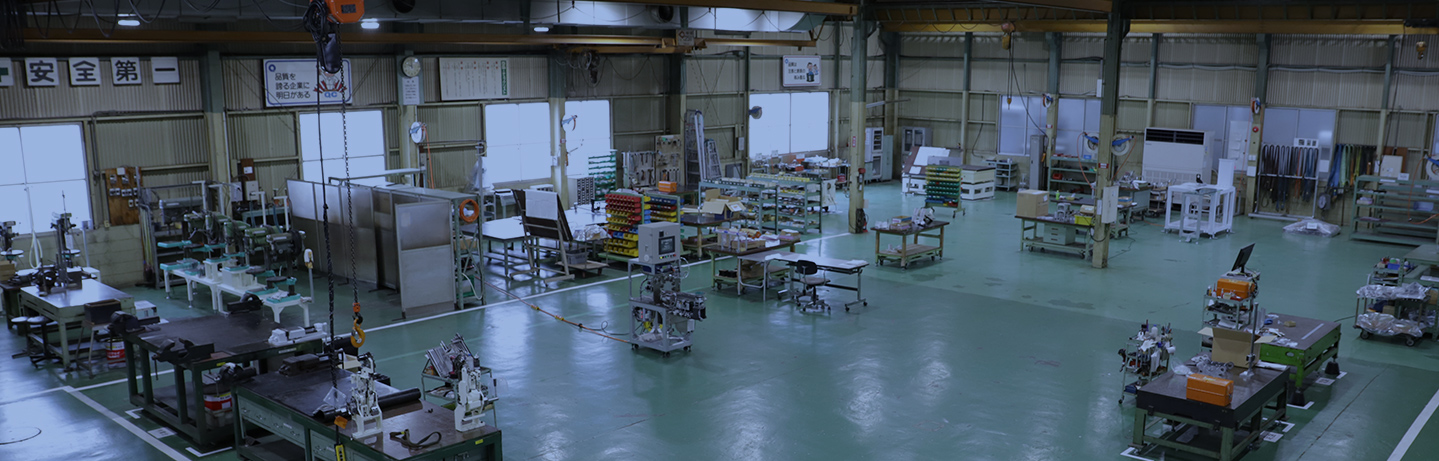
実績一覧
実績一覧表
- ホーム
- 実績一覧表